Embroidery and needlework is a craft that instantly works as an identifier for a particular region or nation whether it is the
chikankari of Lucknow or the bright and geometric Cossack stitches of the Russian region. In India, we are blessed to have a multitude of regional influences on sarees that have often given their place of origin a distinct identity. With time and the coming in of industrialization, most of these woven pieces of art are becoming harder to find.
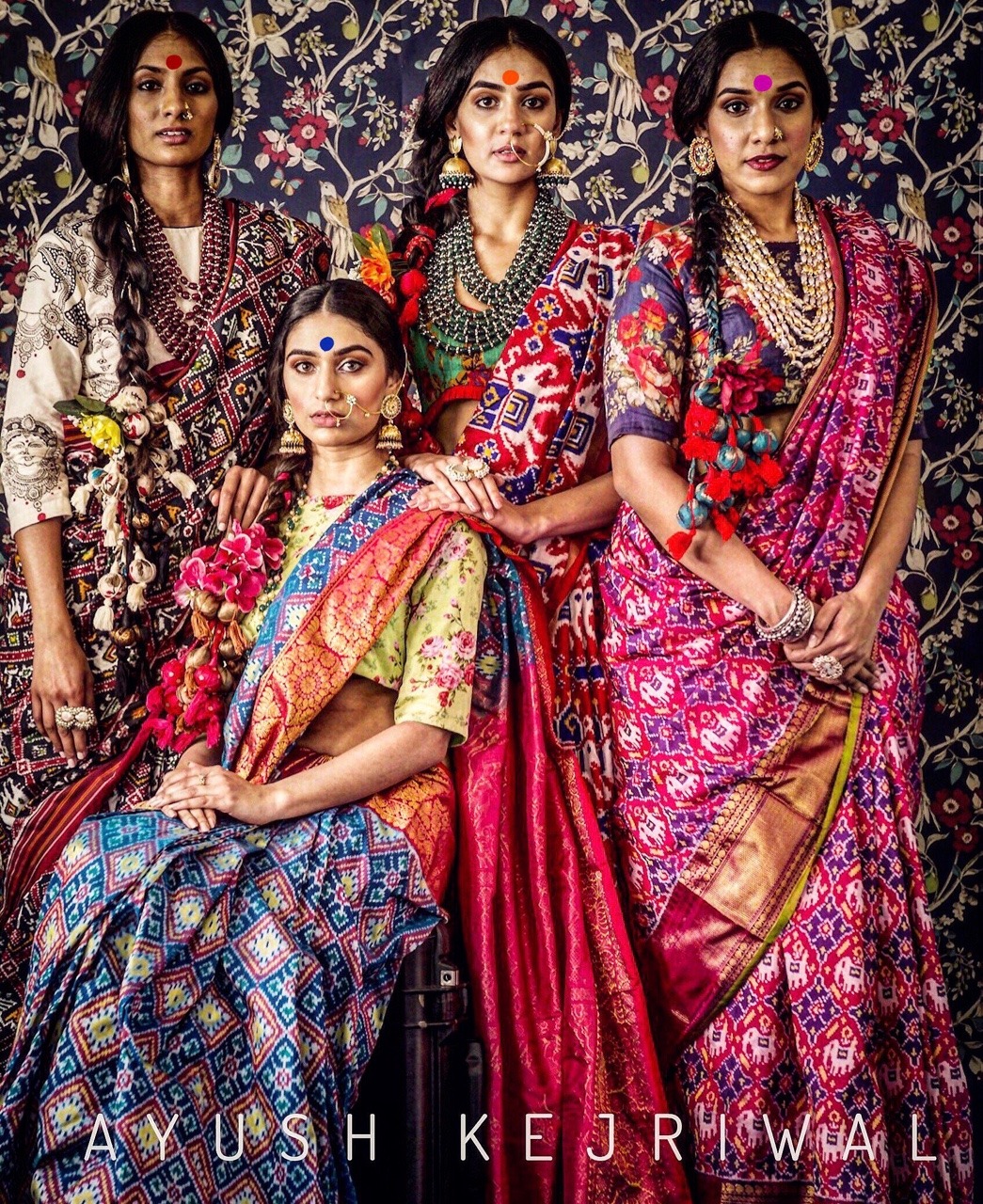
This wedding season, revive a traditional art form and stand out from the crowd. Here are 5 types of silk sarees that are a must-have in any bride's trousseau:
- Banarasi
Banarasis have been a part of Indian wedding traditions since ages. Katans, Jamdanis, Jamavars, Koras and handloom silks in jewel-toned hues are irresistible for any bride. Varanasi, an ancient city on the confluence of the holy Ganga is famous for these sarees. Banarasi sarees feature the best quality silk fabric and brocade weave, which are used to craft woven motifs, patterns, and other intricacies. A tad on the heavy side, but then that is what the bride is for - standing out from the crowd.
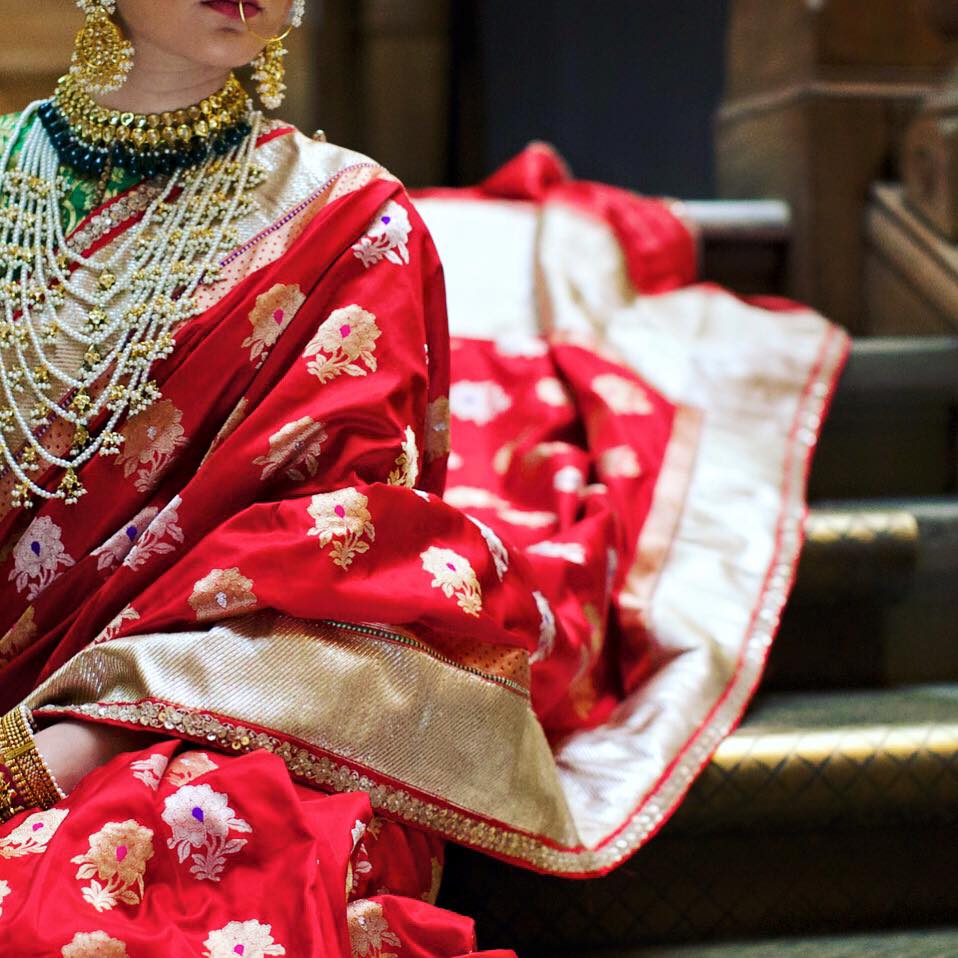
Banarasi
The Banarasi saree is not just a must-have in every bride's trousseau, but it is a famed souvenir from India that is treasured by people across the world. The weavers of Banaras have existed since the time of the Rig Veda. The famous Creation Hymn describes creation as an act of weaving: “Weave forward, weave backward, they say, as they sit by the loom stretched tight. The man stretches the warp and draws the weft. The man has spread it out upon this dome of the sky. These are the pegs that are fastened in place. They made the
Sama melodies into shuttles for weaving.” The sarees of Banaras have been influenced heavily by Roman invasions, the Mughals as well as the Persians and Chinese traders. From kimkhwab to jaamdani, tassar, rangkaadh, shikargah, kadhua… silver work, gold zari… heavy and light, delicate and ‘fancy’ - the variety is stunning.
The classic Banarasi sari, born after craftsmen migrated to Banaras (Varanasi) from Persia during Mughal times, is today fighting against the fake Banarasis made of Chinese silk and plastic zari on a machine called the power loom. The weavers of Varanasi are internationally renowned for creating some of the most beautiful masterpieces. These weavers work hard on designing these sarees to keep its individuality. The masterpiece of the sari needs 15 days to a one month and sometimes up to six months to complete. A less known fact is that not all showrooms in Banaras or anywhere in India can claim to sell a real Banarasi. The real work is done by the
gaddidars, the wholesale operators who have emerged from a family tradition of weaving.
Remember this while buying a banarasi saree - powerloom may be cheaper, but it is definitely not the real thing.
- Patola
Patola saris are made in the Patan region of Gujarat. These expensive silk sarees were once only worn by royalty and aristocracy. The weave is a double ikat, usually made from silk and are renowned for their colorful diversity and geometrical style. Patola-weaving is a closely guarded family tradition. There are only three families left in Patan that weave these highly prized double ikat saris.
Patola was always coveted – a folk song sung by women for their traveling husbands in Gujarat: “O my dear! Do bring the precious Patola from Patan for me.” The same song in Gujarati: “Chhelaji re, mare hatu Patan thi Patola mongha lavjo.”
Epics like the Ramayan and Narsinha Puran refer to the use of Patola in marriage ceremonies as an auspicious garment. This traditional art received great patronage during the Chalukya period. It is said that traveller Ibn Batuta presented kings with Patolas to gain their friendship. These also found their way to Malaysia, Indonesia and other South-East Asian countries.
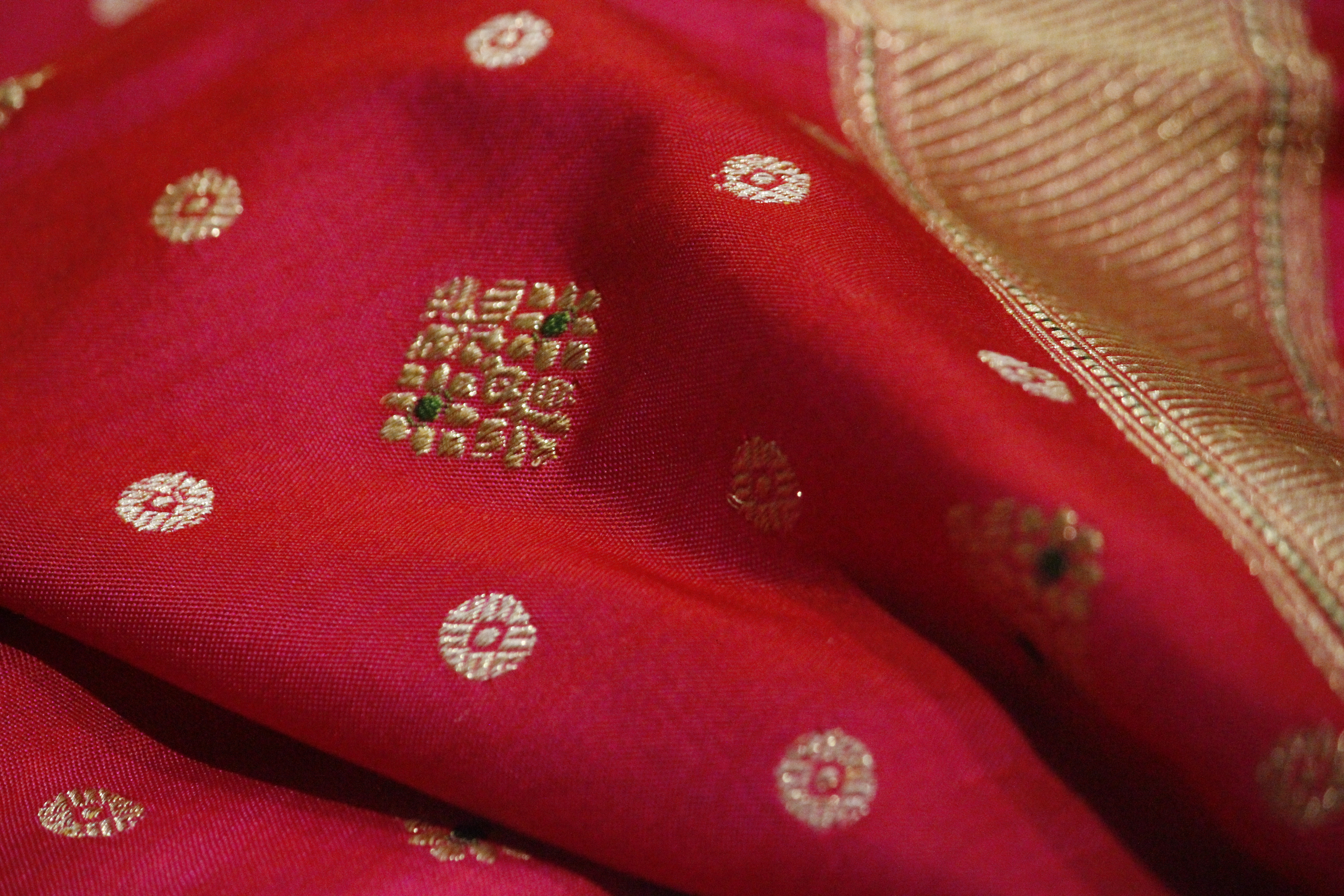
patola
The weaver makes the special Patola loom and colouring from indigenous natural materials. The main patola designs are pan bhat – leaf design, ratan chok bhat – jewel square, popat kunjar bhat – parrot and elephant design, nari kunjar bhat – woman and elephant design, chhabadi bhat – basket design and vohra gali bhat – pattern preferred by Vohra Muslims. The designs, which may comprise floral or animal motifs, are first drawn on paper to achieve accuracy and accordingly warp and weft are tied into knots and then dyed into different colours. It involves complicated calculations, the base of the sari is totally stood on geometrical creations. The process of making of the sari starts with dyeing the wrap and the weft yarns according to the planned pattern of the final cloth. The weaving needs care in uniting a particular colour in the weft with that in the warp. The procedure is not only costly, but also time-consuming. Only 5 to 6 inches a day can be woven to achieve a smooth and identical finish on both sides of the fabric. The magnificent coloured highly prized Patola saree takes nearly one to two years to complete and is preserved as an heirloom.
- Kasuti
The kasuti style of embroidery (mostly done on sarees) from Dharwad is a rather less known form of embroidery. It consists of interwoven geometric patterns that make up for this interesting design. This style originated way back in the 7th century in the lands of Western Karnataka in the regions of Dharwad. It has mostly been adapted from the temple designs and architectural musings of the surroundings. 'Kai’ in Kannada means hand and 'Suti’ means cotton - so 'Kasuti' means handwork of cotton thread. The geometrical patterns are close folded and, formed out of four stitches known as gavanti, muragi, nevgi and menthe. These stitches are completely based on the thread count method and are equidistant.
Kasuti work is generally done on Ilkal
sarees. Ilkal
sarees are made in the Ilkal town of Bagalkot district of Karnataka. Hand woven silk sarees in bright jewel hues make this design look amazing and different. The artisans work hard before engaging in this embroidery. They insist on drawing out the designs on paper before they can weave it on a saree.
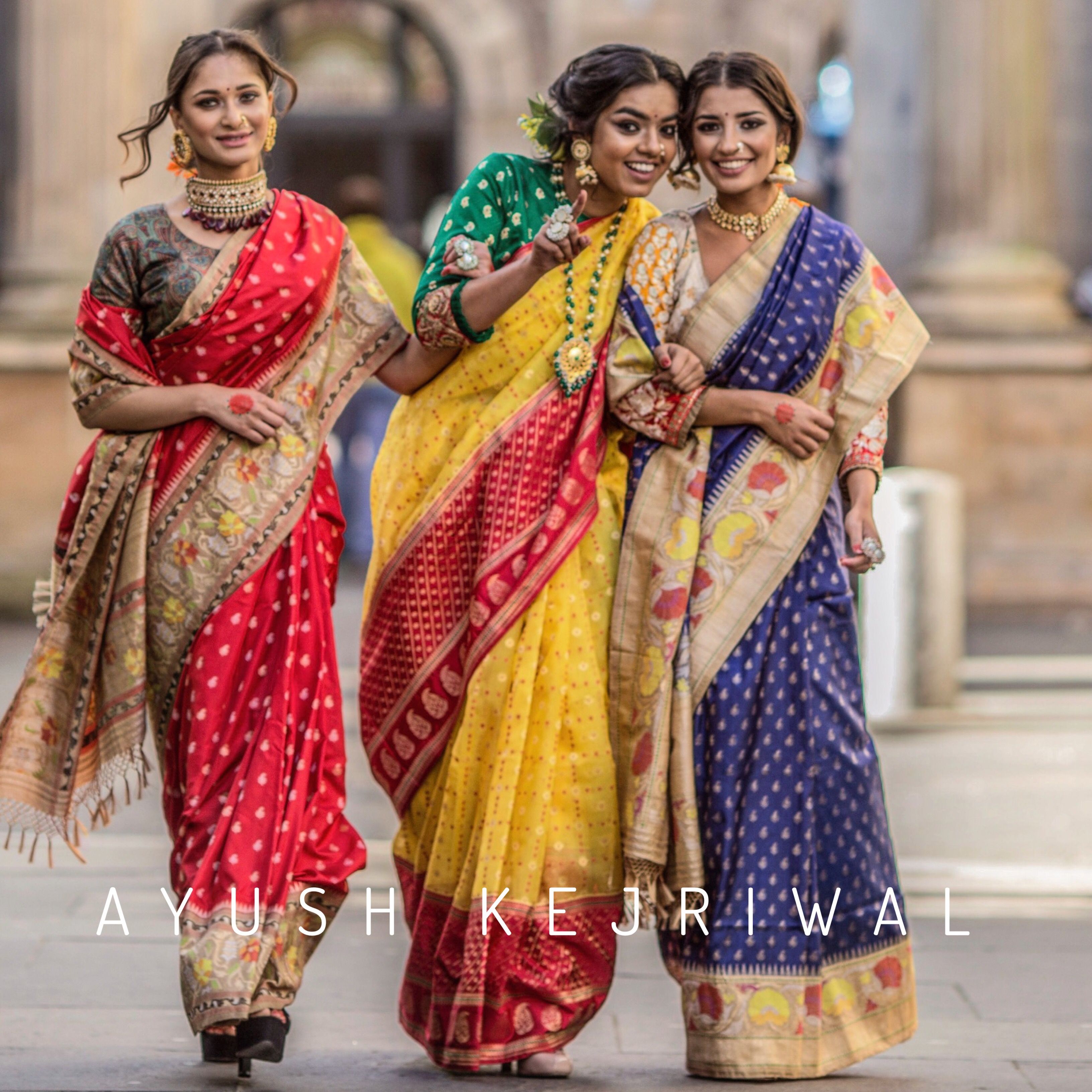
kasuti
It has motifs like palanquins, elephants, tulsi kattas, lotus, parrots, and small birds. Kasuti work is generally done on Ilkal sarees. Ilkal sarees are made in the Ilkal town of Bagalkot district of Karnataka. The uniqueness of the sari stems from weaving the warp (lengthwise threads) in cotton and those in the pallu and the border area in art silk or pure silk. This means that the warp of each and every sari has to be prepared specially. The warp threads of the body and warp threads of the pallu and borders are linked together by loops locally addressed as “Topa Teni” Technique.
The pallu of this type of silk sarees consists of designs like temple borders which are embellished with motifs which are generally embroidered in geometric shapes and it ends with patterns like comb, forts, or mountain ranges. The body of the saree also comprises of small motifs of embroidery.
- Mekhela Chador
Handwoven
Mekhela chador is an unparalleled pride of Assam. It consists of two pieces of cloth, draped on the top and bottom, which is the traditional attire worn by the women of Assam. The bottom half of this unique dress is called the ‘
mekhela’ which is cylindrical in shape and is worn waist downwards over a petticoat. The main hub of these Mekhela Chadors is a tiny town called Sualkuchi, situated at just 35 kilometers from the city of Guwahati. Sualkuchi is responsible for the majority of the Mekhela Chadors that are being manufactured in Assam. The Mekhela Chadors made in this small town are highly sought after by women in Assam and the rest of India, alike. The Mekhela Chadors are usually found in three varieties and are differentiated on the basis of the silk being used in its manufacturing. The different varieties of Mekhela Chadors are:
- Muga Mekhela Chador: These Mekhela Chadors are the ones that are being made by using the Muga Silk and are believed to be so durable that they often outlive their owners.
- Eri Mekhela Chador: These Mekhela Chadors are the ones that are being made by using the Eri Silk and are usually soft and warm in nature.
- Pat Mekhela Chador: These Mekhela Chadors are the ones that are being made by using the Pat Silk and are generally white in colour, ranging from brilliant white to off-white.
Mekhla chador
The Mekhela Chadors made of Muga or Pat Silk are usually the more fancied ones and can be worn almost throughout the year at special occasions. The ones made of Eri Silk are soft and warm in nature and hence are better suited for colder climatic conditions whereas the Cotton ones are best suited for daily usage at home.
This type of silk sarees is ideal for the bride that wants to truly stand out without getting overshadowed by bling.
- Baluchari
Originally woven in the Murshidabad district of West Bengal, and today in Bishnupur,
balucharis are rich silk sarees characterized by intricate weaving in the pallav and borders, depicting stories from epics, historical and religious texts. The grandeur of a baluchari is further enhanced when the weaving is in gold colour, giving it the name ‘swarnachari’. The opulence of baluchari sarees make them apt for wearing at festivals & weddings. It is a hand woven saree using richly dyed silk, with intricate motifs depicting Indian mythology woven onto its large ‘pallu’. Baluchari takes a week to be woven, and the craftsmen are largely centered in Murshidabad.
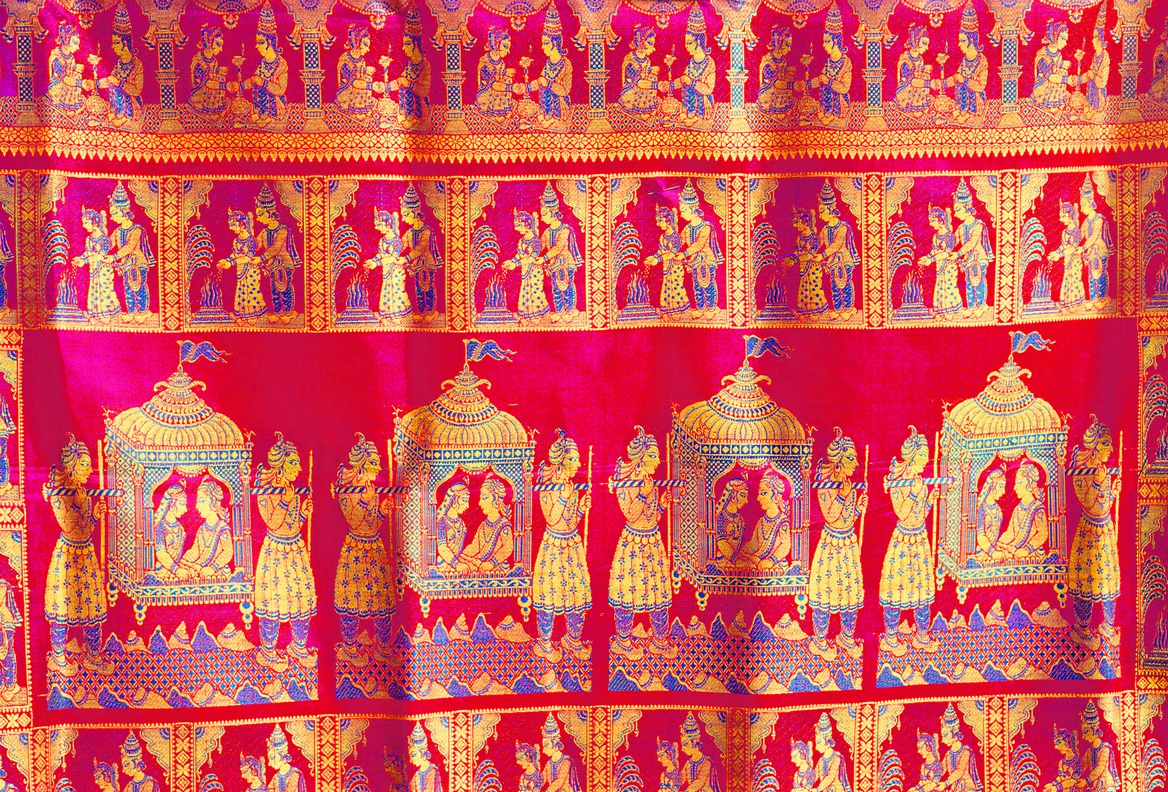
Baluchari
The simplest balucharis have resham threads in a single colour to weave the entire pattern. Meenakari balucharis have threads in two or more colours with attractive meenakari work that further brightens the patterns. However, the Swarachuri balucharis are the most gorgeous balucharis, woven with gold (swarna) or silver coloured threads (often with meenakari work in another colour) that illuminate the patterns to a much larger extent. The Baluchari sarees are known for their intricate designs and handwork that are mainly inspired from the Ramayana and Mahabharata, with the story of Lord Krishna teaching Arjuna about the Bhagawat Gita being most popular. They are indeed collectors’ items and are often passed down from one generation to the other.
To know such interesting information on Indian fabric and textile, follow us on
Facebook,
Instagram, and
Twitter. Download the magazine
Spunky Indian to read exclusive stories.